We explain what total quality is, what its characteristics and its principles are. Plus, the cause and effect diagram, and more.
What is total quality?
Total quality is a type of management aimed at the search for quality in the different processes of an organization , with the ultimate goal of achieving the highest customer satisfaction. Total quality is a continuous improvement strategy that reaches all areas, staff and customers of a company .
In the 1960s, the Japanese industrial chemist and business administrator Kaoru Ishikawa was the one who created this business quality system and defined it as: “A philosophy of the organization, in which all its members study, practice, participate and promote improvement. keep going".
At present, total quality consists of a set of strategies for the management of organizations and is based on principles. The objective is to satisfy in the most balanced way and with the highest possible level of quality to all those involved, such as the company, its employees or customers.
Total quality characteristics
Among the main characteristics of total quality management, the following stand out:
- Focus on the customer. It refers to the fact that a large part of the company's efforts are dedicated to satisfying customer expectations, both for the offer of products and services.
- Leadership aligned with the objectives of the organization. It refers to the fact that the objectives of the company must be aligned with the philosophy of continuous improvement.
- Importance of internal employees. It refers to the fact that the development and growth of the people within the company is as important as giving place to their opinion.
- Management based on continuous improvement. It refers to the fact that each decision-making and management performance must act from questioning and prior self-analysis, in order to maintain continuous improvement.
- Importance of external employees. It refers to the fact that customers, suppliers and other personnel external to the company are of equal importance as its internal employees. Encouraging continuous improvement in the relationship with each part is essential to achieve a total quality level.
Principles of total quality
The fundamental principles on which total quality management is based are:
- Quality can and must be quantified, controlled and improved .
- Quality improvement must be continuous .
- Every company has clients and is, at the same time, a supplier to another company.
- The processes are usually the problems , not the employees themselves.
- All employees have an influence on the achievement of quality, so their participation and opinion are necessary.
- Problems must be avoided as well as fixed.
- Management must plan and manage quality improvement strategies.
- Decision-making must be based on facts .
Cause and effect diagram
One of the total quality tools proposed by Kaoru Ishikawa was the cause and effect diagram, also known as the herringbone diagram. It consists of a scheme that allows analyzing the causes of a problem taking into account various factors that intervene throughout the process, not just the consequence itself.
The diagram allows you to visualize all the factors that may have caused the problem, to analyze and corroborate which was the point factor that acted as a trigger. The solution will be to eliminate the cause, to solve the problem.
An example of the application of the cause and effect diagram is to the problem of defective products. Various reasons can be analyzed, such as:
- The machinery: The equipment may be damaged or lacking in maintenance.
- The methods: The lack of quality control or the need to optimize production times.
- The raw material : The quality is inferior or the material came defective.
Other models of total quality
In addition to the cause and effect diagram prepared by Ishikawa, there are other more current tools that are used in total quality management. The main tools include:
- Staff evaluation instruments . They make it possible to identify various causes, both personal and in the business environment, that interfere with the employee's performance.
- Quality model of Malcolm Baldrige. It allows to improve the performance and innovation capacity of companies, through questioning and self-evaluation carried out periodically.
- Lists of good practices. They allow to reinforce the business philosophy based on continuous improvement. Good practices can be written down in a document, sent as a reminder by e-mail, or form part of the posters in various areas of the company.
- External certifications. They allow to have the endorsement of the company's quality level, through certifications issued by external audit entities or by organizations specialized in controlling the company's quality standards.
The above content published at Collaborative Research Group is for informational and educational purposes only and has been developed by referring reliable sources and recommendations from technology experts. We do not have any contact with official entities nor do we intend to replace the information that they emit.
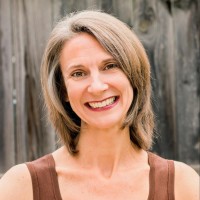
Anas is an editor of a prestigious publishing company in the United States. She studied Mathematics in Arizona. Anas is also a teacher and one of her long-term goals is to build an institution that offers free education to everyone who are financially not stable. .
Leave a reply
Your email address will not be published. Required fields are marked *Recent post
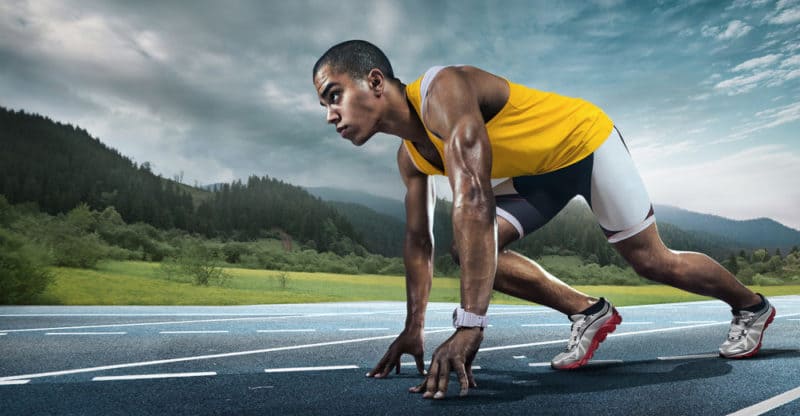
Sport: What Is It, Types, Risks, Features, Characteristics and Examples
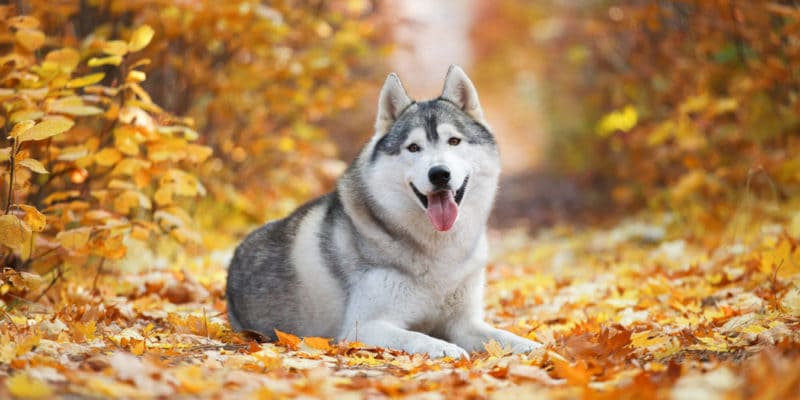
Dogs: Emergence, Features, Characteristics, Feeding and Breeds
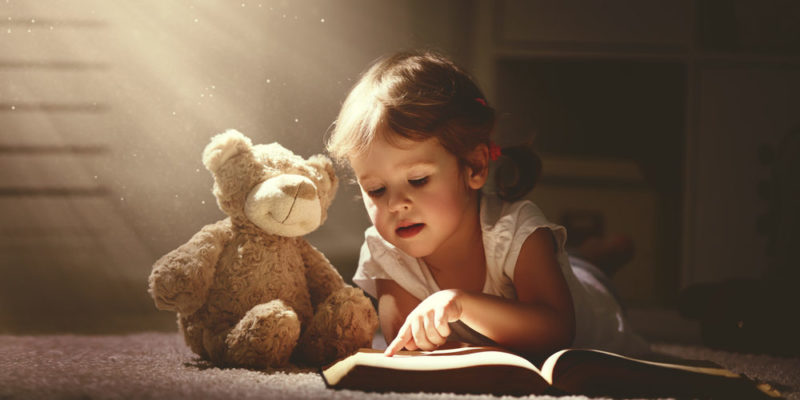
Story: Definition, Elements, Structure, Features and Characteristics
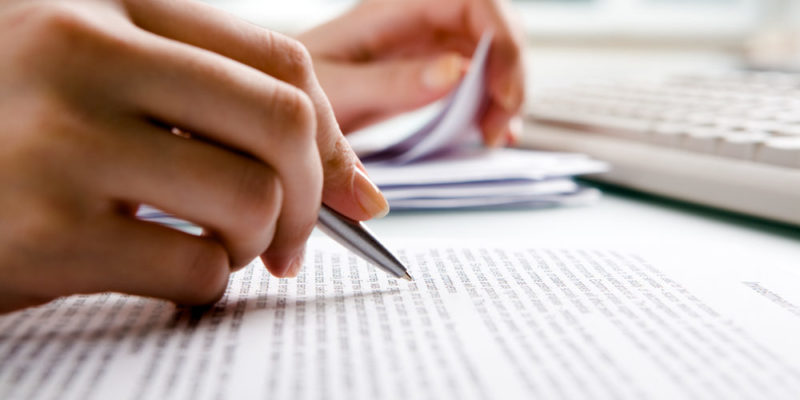